Gyratory Reciprocating Screener for Efficient Material Separation
Explore our Gyratory Reciprocating Screener, designed for efficient material separation in industrial applications. Messe365 provides advanced solutions that enhance screening performance and processing efficiency.
Types and Applications of Gyratory Reciprocating Screeners
Gyratory reciprocating screeners are effective machines used for screening and separating materials in various industries. They operate through gyratory motion, which significantly improves efficiency in material processing. Gyratory equipment, including Rotex screeners, is known for its innovative designs that enhance performance across different applications.
What are the Different Types of Gyratory Reciprocating Screeners?
There are several types of gyratory reciprocating screeners designed to meet specific industrial needs:
- Rotex Screeners: These are highly recognised for their effective gyratory motion and sturdy build, making them suitable for heavy-duty tasks.
- Circular Screeners: They utilise a circular motion, which is beneficial for applications requiring quick and high-volume screening.
- Linear Screeners: These employ a linear motion, being ideal for finer particle separation.
Each type of gyratory screener offers distinct advantages, improving efficiency and material handling capabilities for diverse industrial uses.
How do Gyratory Reciprocating Screeners Work?
The functioning of gyratory reciprocating screeners involves a blend of gyratory and reciprocating motions. Key principles include:
- Conveyors and Feed Systems: Materials are systematically introduced onto the screening surface via an integrated conveyor system, ensuring steady flow.
- Mechanical Drive: A mechanical drive powers the screens, creating the necessary gyratory motion.
- Reciprocating Motion: This motion ensures even distribution of materials on the screening surface, facilitating proper separation.
- Performance Metrics: With sound engineering design, these machines achieve optimal performance by maintaining specific operational parameters tailored to the materials involved.
This combination enables effective screening and processing capabilities, resulting in higher productivity.
What are the Common Applications for Gyratory Reciprocating Screeners?
Gyratory screeners serve numerous applications across different sectors, including:
- Agriculture: Used for seed cleaning and grading.
- Food Processing: Helps in quality control for grains and powders.
- Chemicals: Assists in sorting and separating chemicals in manufacturing.
- Mining: Facilitates aggregate screening and ore processing.
- Pharmaceutical: Ensures purity and size classification of medicinal powders.
- Recycling: Aids in waste separation technology for material recovery.
- Bulk Material Handling: Effectively manages large volumes of bulk materials.
These varied applications highlight the importance of gyratory reciprocating screeners in enhancing operational efficiency across multiple industries.
How to Choose the Right Gyratory Reciprocating Screener
Choosing the right gyratory reciprocating screener involves several key factors:
- Application Requirements: Assess the specific needs of your operation to find the best screener match.
- Material Characteristics: Understand the physical properties of the materials being processed, such as size, weight, and moisture content.
- Efficiency Goals: Evaluate your desired throughput and screening efficiency to ensure satisfactory performance.
- Heavy-Duty Needs: For demanding applications, opt for heavy-duty screeners that promise durability and reliability.
- Customer Service and Support: Look for manufacturers or suppliers like Messe365 Online Machine Evaluation that offer robust customer service and solutions.
By considering these elements, you can effectively select a gyratory reciprocating screener that boosts productivity and meets your operational standards.
For further inquiries or detailed technical specifications, feel free to Request a Manual or Learn More about our offerings at Messe365.
Advantages and Disadvantages of Gyratory Reciprocating Screeners
Gyratory reciprocating screeners are highly regarded for their effectiveness in industrial applications, particularly within the food and pharmaceutical sectors. They excel in high screening efficiency, allowing for the effective separation of waste and valuable materials. However, while they offer numerous advantages, it’s important to also consider their limitations.
Advantages
- High Screening Efficiency: These screeners greatly improve output by providing superior performance in material sorting.
- Minimal Waste Production: Their design optimises processing, thereby reducing waste significantly.
- Versatile Applications: Ideal for a variety of industries, especially food and pharmaceuticals.
- Low Maintenance Requirements: Compared to other technologies, they generally need less frequent maintenance.
Disadvantages
- Potential Downtime: Regular maintenance is essential, which may lead to interruptions in productivity.
- Design Limitations: Some models might not be appropriate for all materials or specific processing needs.
- Durability Concerns: With time, components can wear down, impacting overall performance.
What are the Benefits of Using Gyratory Reciprocating Screeners?
Using gyratory reciprocating screeners comes with a host of benefits that enhance operational efficiency across different sectors. These features contribute to improved performance and can decrease operational costs.
- Efficiency: Enhanced screening efficiency helps maximise output while reducing waste.
- Effective Material Processing: Suitable for various materials, meeting diverse industry requirements.
- Ideal for Food and Pharmaceuticals: Designed to meet rigorous industry standards, ensuring safety and reliability.
- Innovative Solutions: Utilising advanced engineering techniques ensures optimal results.
These advantages enable businesses to realise significant improvements in operations.
What are the Limitations of Gyratory Reciprocating Screeners?
Even though gyratory reciprocating screeners are effective, there are limitations to consider when choosing equipment for specific applications.
- Downtime During Maintenance: Regular upkeep is necessary, leading to potential downtime.
- Design Constraints: Certain models may have features that restrict their application versatility.
- Possible Performance Issues: Factors like wear and tear can diminish processing efficiency over time.
- Required Spare Parts: The availability of spare parts can influence repair times and ongoing performance.
Recognising these limitations aids in making well-informed decisions regarding equipment selection.
How to Optimize Gyratory Reciprocating Screener Performance
To optimise the performance of gyratory reciprocating screeners, consider implementing several strategies:
- Routine Maintenance: Establish a consistent maintenance schedule to keep performance high and reduce downtime.
- Parameter Adjustments: Tweak operating parameters like vibration frequency and angle to align with material characteristics.
- Training for Operators: Provide operators with comprehensive training on the machine's capabilities to boost operational effectiveness.
- Use of Quality Spare Parts: Opt for genuine spare parts to maintain the screener’s integrity and extend its lifespan.
Implementing these practices helps achieve greater efficiency and effectiveness in material processing.
Maintenance and Troubleshooting Tips for Gyratory Reciprocating Screeners
Effective maintenance and troubleshooting are key to maximising the functionality of gyratory reciprocating screeners. Here are essential tips:
- Regular Inspections: Perform routine checks for wear and damage on critical components.
- Keep Spare Parts Handy: Maintain a stock of essential spare parts to minimise downtime during repairs.
- Document Performance: Track performance metrics to identify trends and address issues proactively.
- Consult Manuals: Always refer to the manufacturer’s manual for troubleshooting guidance and maintenance requirements.
Following these recommendations will help ensure the screener operates efficiently and reliably, ultimately enhancing overall productivity.
Industry Innovations and Trends in Gyratory Reciprocating Screeners
Gyratory reciprocating screeners are at the forefront of mechanical screening technology, offering effective solutions for a diverse range of industrial uses. Leading companies like Rotex and Andritz have significantly contributed to the advancement of gyratory screeners by introducing innovative technologies. These developments aim to boost efficiency, sustainability, and reliability in operations, meeting the growing needs of sectors such as waste recycling, chemicals, food processing, and agriculture.
What are the Latest Advancements in Gyratory Reciprocating Screener Technology?
The latest advancements in gyratory reciprocating screener technology focus on enhancing performance through various means. Some key features include:
- Smart Automation: Integrating automation for real-time performance monitoring.
- Improved Energy Efficiency: New drive systems that reduce maintenance and energy use.
- Modular Configurations: Designs that allow for easy upgrades based on specific processing requirements.
- Sustainable Operations: Implementing practices that lower energy consumption and waste.
These technological advancements are reshaping mechanical screening technology, allowing industries to operate with greater productivity while minimising their environmental footprint.
How are Gyratory Reciprocating Screeners Being Used in Emerging Applications?
Gyratory reciprocating screeners are increasingly utilised across various emerging applications, including:
- Waste Recycling: They efficiently separate recyclables from waste, improving recovery rates.
- Chemicals: Ensuring uniform particle sizes for quality control in production.
- Food Processing: Employed for sieving and grading food products to uphold safety regulations.
- Agriculture: Used in cleaning seeds and grains, leading to better crop yields.
These applications showcase how gyratory screeners enhance operational efficiency and effectiveness in bulk material handling.
What are the Future Trends in Gyratory Reciprocating Screener Development?
Looking ahead, several trends will shape the development of gyratory reciprocating screeners:
- Sustainability Focus: Prioritising environmentally friendly practices and energy-efficient designs.
- Material Innovations: Utilising advanced materials to improve durability and reduce wear.
- High-Efficiency Designs: Enhancing performance metrics and reducing energy consumption.
- Integration of Smart Technologies: Incorporating IoT and AI for predictive maintenance and operational improvements.
These trends suggest a movement towards more versatile and efficient machines that can adapt to the demands of modern industries.
Case Studies of Successful Gyratory Reciprocating Screener Implementations
Several businesses have experienced success through implementing gyratory reciprocating screeners. Noteworthy case studies include:
- Trade Solutions Pty Ltd: Enhanced efficiency in waste management, achieving a 30% rise in material recovery rates.
- Various Consulting Firms: Reported increased production speeds and lowered labour costs through the use of advanced gyratory equipment in chemical processing facilities.
These real-world applications demonstrate the effectiveness of gyratory screeners in achieving significant performance improvements across different sectors. For further details or to request a manual on specific models, please visit Messe365 Online Machine Evaluation.
Gyratory Reciprocating Screener
What Is Gyratory Reciprocating Motion ?
Gyratory Reciprocating screening is a newer method of technology combining the benefits of circular, elliptical and reciprocating motions.
The screener gradually transitions along the length of the screener, starting off as purely gyratory motion at the head, moving to elliptical movement in the centre and then reverting back to reciprocating towards the end of the machine.
The circular motion at the feed end, spreads the material across the full width of the screen and hence stratifies the material. The Elliptical motion at the centre enhances product stratification through long stroke elliptical action. The reciprocating motion at the discharge end removes near-size particles improving screening efficiency.
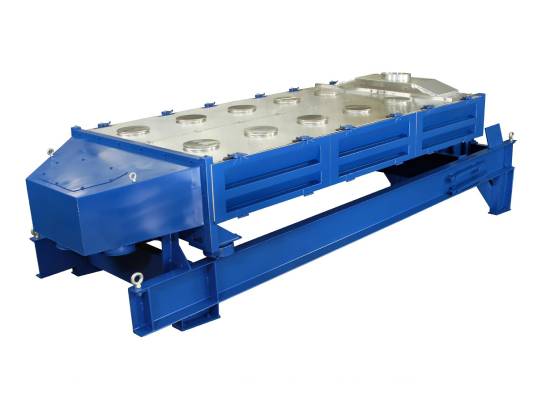
What Are The Benefits ?
Eliminates Screen Blinding
The use of numerous motions reduces the material blinding and when coupled with bouncing balls or other anti-blinding solutions, material blinding is virtually non-existent.
Increased Efficiency
The unique motion is designed to give undersized material maximum opportunities to pass through the mesh openings without the loss of near-size materials and hence reduces efficiency.
Higher Yields
The use of three motions provides efficient distribution, stratification and separation resulting in higher yields and less rejection of good material.
Versatile
Gyratory Reciprocating Screeners are unique in their method of vibrations and are extremely versatile, widely used in chemical, agricultural, food, medicine, mineral, plastic and recycling industries plus many more.